Although cremation machines produced by different manufacturers vary in model and specifications, their basic structure is generally the same.
The structure of a Eco-friendly cremation equipment in China typically includes the following parts: front hall preparation door system, cremation furnace (with primary and secondary combustion chambers), body/ashes transfer system, fuel supply and combustion system, exhaust system, and control system. Modern cremation machines may also come equipped with an “exhaust gas purification system.”
2.1 Front Hall Preparation Door System
Definition: The front hall preparation door system is an electric door installed between the front hall and the preparation room.
Function: It separates the equipment in the front hall from the cremation room, creating an elegant and refined front hall as a decorative door structure.
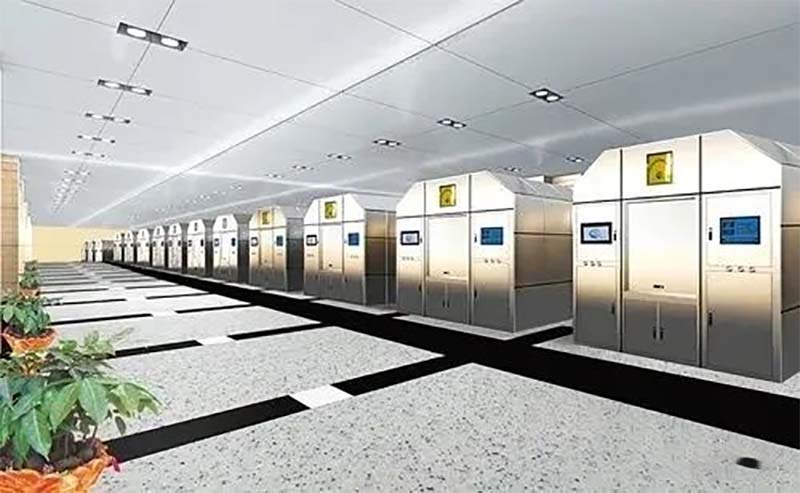
Components: This system consists of the door body, track, and transmission device. The door frame is made of square steel, with a 1mm stainless steel outer layer. Typically, the door has two leaves that open outward, although single-door designs are available for narrow cremation rooms. Different transmission mechanisms are used for opening and closing the door, including belt-driven, chain-driven, and link-driven types. Belt-driven doors have a simple structure, requiring only a motor, a reducer, and two rollers for stable movement, although the belt may loosen over time and require adjustment. Chain-driven doors are more reliable than belt-driven types, with smoother motion and less wear. Link-driven doors also move smoothly, are quieter, and have a simpler structure.
2.2 Cremation Furnace
The cremation furnace is the "heart" of the cremation machine system and the core component for evaluating cremation machine performance. The main performance indicators of a cremation machine include energy consumption per cremation, cremation time per body, combustion temperature, emissions of pollutants in exhaust gases, and heat retention.
- Typical Furnace Structure: A cremation furnace generally includes an outer casing, steel structure, brick lining, door and opening mechanism, operation door, ash removal device, and ash door. Bodies are positioned longitudinally and fed into the furnace using a setup of large and small carts. The large cart, driven by a motor and reducer, moves forward and backward, carrying the small cart along with it. The small cart, also motor-driven, moves in and out of the furnace, transporting the refractory bed that holds the body.
- Multifunctional Double-Deck Cart: One furnace can be equipped with a multifunctional double-deck cart with lateral cooling capability. This cart, driven by a motor and reducer, moves bodies in and out of the furnace and preparation room, with the refractory bed moving along with the elevator. Once inside the furnace, the bed remains for cremation, cooling, and ash collection.
- Double Refractory Bed Cart: This cart design includes two small carts (each with its own refractory bed) that can be alternated vertically or laterally. The large cart is equipped with central and in-furnace rollers, as well as a lift mechanism, allowing the small cart to move longitudinally and vertically. Positioning of movement is controlled by a limit switch.
- Composite Cart: Comprising a fixed main cart and a movable small cart, this setup features an arm-type bidirectional ash collector and a cooling device similar to the double refractory bed design.
- Single-Refractory Bed Cart: The single refractory bed cart features a cooling system similar to the first configuration. The design of corpse transfer carts has continued to evolve, offering various configurations.
2.3 Fuel Supply and Combustion System
Cremation machine fuels are available in solid, liquid, and gaseous forms. Early cremation furnaces in China used coal, but most now use light diesel. In areas with access to natural gas, liquefied petroleum gas, or city gas, gaseous fuels are also used. Here, we provide an overview of the fuel supply and combustion system for light diesel fuel.
The fuel supply and combustion system delivers fuel to the cremation machine and ensures efficient combustion within the furnace. This system consists of an oil tank, pipelines, filters, valves (manual and electric), oil pump, burner, air supply piping, and air valve. Its purpose is to guarantee adequate and complete combustion to meet the furnace's heat (temperature) requirements. The system's main technical requirements include a steady fuel supply, leak-proof tanks and pipelines, sensitive valve controls, adjustable burners, and high combustion efficiency.
Burners are fuel combustion devices. In coal-fueled furnaces, they are known as "combustion chambers." In oil-fueled furnaces, they are called "spray nozzles," and in gas-fueled furnaces, they are referred to as "burners."
For liquid and gaseous fuel burners, a flame monitoring and automatic ignition system is installed to ensure automatic ignition and flame monitoring.
2.5 Jet Exhaust System
The jet exhaust system operates on the principle of gas stream adhesion, with a high-pressure jet air pipe inside the exhaust stack, using high-pressure air from the blower to discharge exhaust gases. This high-pressure air quickly entrains the surrounding smoke and gases out to the atmosphere. The main features are as follows:
- The draw strength of the jet exhaust stack depends only on the flow rate and density of the high-pressure medium. It is especially effective in situations with low exhaust volume where a chimney is not desired.
- The jet exhaust fan can operate with a standalone blower or draw on high-pressure air from the supply system, consuming less power than traditional induced draft fans.
- The low-temperature, high-pressure jet air dilutes high-temperature gases, thus imposing no special material requirements on the exhaust stack.
- This system is suitable for applications with low exhaust resistance demands; systems with higher resistance requirements should use an induced draft fan.
- The jet exhaust system consists of an exhaust pipe, nozzle, and blower.
2.6 Control System
The control system of a cremation machine encompasses all electrical controls and monitoring instruments. It has three main functions: 1) power control (or electric drive), 2) display and control of operational parameters (or information control), and 3) time-based control of mechanical movements (or programmed timing). Additionally, there is a safety function for protecting the system, equipment, and personnel. This safety function can be configured separately or integrated within the primary controls.
- Power Control: The power control, or electric drive, manages the main power mechanisms, including fans and fuel pumps. These motors require specific startup circuits and connection methods due to their large power requirements.
- Operational Parameter Display and Control: This information control system displays and regulates key parameters, such as combustion chamber temperature and pressure. High-temperature ceramic thermocouples measure temperature, generating voltage (mV) signals for computer display and control. Pressure sensors produce current signals (mA) for display and control.
- Time-Based Control of Mechanical Movements: This control includes the lateral and longitudinal movement of the body cart, up-and-down motion of the furnace door, and positioning of the damper. The purpose is to safely transport the body to the combustion chamber while halting burners and airflow temporarily, ensuring safety for personnel and equipment. These processes are controlled by either a computer program or an interlock system with limit switches.
The control system generally allows automatic and manual operation modes, ensuring safety, reliability, easy operation, and low maintenance rates.